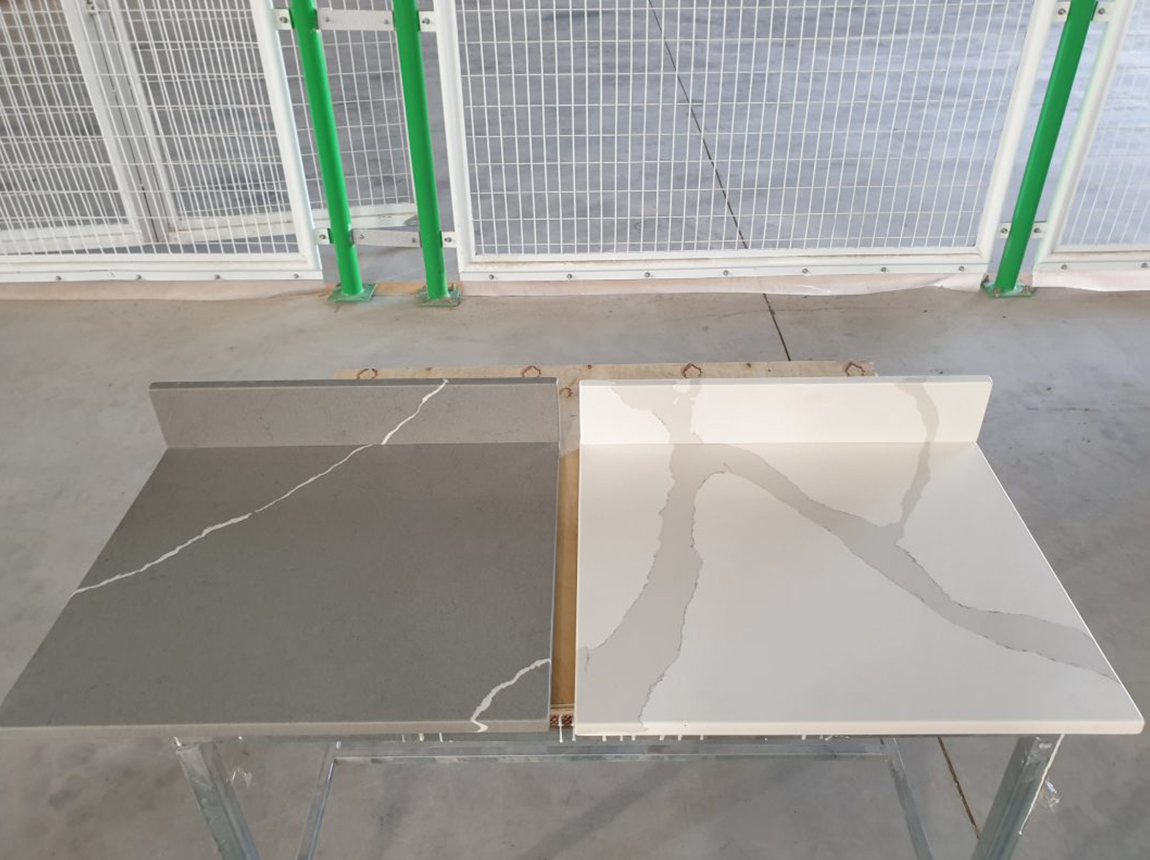
The process of manufacturing quartz, also known as engineered quartz or quartz stone, involves several steps that combine natural quartz crystals with resins, polymers, and pigments. This process allows for the creation of a durable and aesthetically pleasing material that can be used for various applications, such as countertops, flooring, and wall cladding. Here are the key steps involved in the manufacturing of quartz:
1.Raw Material Selection: The first step is selecting high-quality natural quartz crystals. These crystals are usually mined from quarries or obtained from rock deposits. The selected quartz must have a high purity level to ensure the final product’s quality and consistency.
2. Crushing and Blending: The selected quartz crystals are crushed into small, uniform particles. This process helps in creating a homogeneous mixture and ensures that the final product has a consistent appearance and texture. Additionally, other additives like resins, polymers, and pigments are introduced at this stage to impart specific properties and colors to the engineered quartz.
3. Mixing: The crushed quartz particles and the additives are thoroughly mixed together. The exact composition and proportions of the ingredients are carefully controlled to achieve the desired properties and appearance of the final product.
4. Vacuum Vibrating: The mixture is then poured into a mold and subjected to a vacuum vibrating process. This step removes any air bubbles and ensures that the mixture is compact and free of voids.
5. Pressing: The compacted mixture is transferred to a specialized press, where it is subjected to high-pressure and high-temperature conditions. This process, known as “pressing,” compacts the materials even further and helps in binding the quartz crystals together with the resins and polymers.
6. Curing: After the pressing process, the slab is cured in an oven at high temperatures. The heat triggers a chemical reaction that causes the resins to harden and bind the quartz particles together permanently.
7. Trimming and Calibration: Once the curing process is complete, the engineered quartz slab is trimmed and calibrated to achieve the desired thickness and flatness. This ensures that the slabs are uniform and ready for further processing and installation.
8. Surface Treatment: Depending on the intended application, the surface of the quartz slab may undergo additional treatments. For instance, a polished finish is achieved by grinding and polishing the surface to a high gloss. Other finishes like honed, brushed, or textured surfaces can also be applied.
9. Quality Control: Throughout the manufacturing process, quality control measures are implemented to ensure that the engineered quartz meets the required standards for durability, appearance, and consistency.
10. Distribution and Installation: Finally, the finished quartz slabs are packaged and distributed to suppliers, fabricators, and retailers for installation in various projects, such as residential and commercial spaces.
The manufacturing process for quartz is highly controlled to produce a reliable and consistent material that offers the desired properties and aesthetics for a wide range of applications.